Boiler tube repairs and welding
Boiler tube repairs and welding
The boiler tube is a type of seamless tube. The manufacturing method is the same as that of the seamless pipe, but there are strict requirements for the steel used in the manufacture of the steel pipe. According to the use temperature, it can be divided into two types: general boiler tube and high pressure boiler tube.
The service life of boiler tubes is limited, so boiler tubes need to be replaced and repaired regularly.
How to repairs the boiler tube?
If the boiler tube is used for a long time, it will leak and block. In order not to affect the use of the boiler, we have to replace some of the boiler tubes, but if there is a thin wall in the boiler tubes, it is necessary to replace all the tubes of the boiler.
The specific number of boiler tubes in the boiler is shown in Table 1.
Boiler number | Boiler tube specifications: 63.5mm × 3.5mm | Boiler tube specifications: 45mm × 3.5mm |
1# | 170 | 132 |
The original boiler technical parameters are shown in Table 2:
Table 2
Type of boiler | Fuel exhaust hybrid boiler |
model | Type-7/8 Boiler |
Boiler manufacturer | Fabrica de san carlos, S.A. |
Maximum normal working vapor volume | 800 KG/H |
85% limit steam volume | 842 KG/H |
Amount of steam | 1642 KG/H |
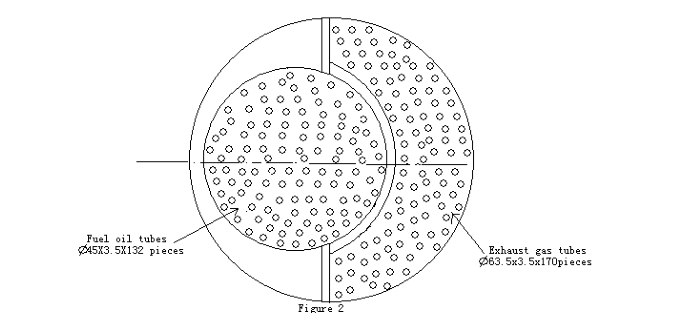
One, boiler tube repair procedures
We will strictly implement the boiler tube overhaul process:
(1) All boiler tubes are removed by gas cutting;
(2) Clean and inspect the tube sheet to make it flat;
(3) Welding consumables, pipe preparation, pipe quality inspection, grinding of new pipe replacement (welding materials and pipes are in accordance with CCS type approved marine boiler pipe GB3087 and SH507 welding rod, see the pipe and welding rod certificate copy);
(4) The pipe is prefabricated, placed in a new pipe, and assembled;
(5) After assembly, check the front and rear ends of the tube to extend 5-6MM, and prepare for welding after passing the test;
(6) The welder holds the corresponding welder certificate approved by CCS, as detailed in the copy of the welder certificate;
(7) When the welding rod is welded, it shall be dried according to the specification of the welding rod; when welding, it shall be installed in the insulated barrel according to the welding rod to keep warm.
(8) Welding the ends of the nozzle, removing the welding slag after welding, and inspecting the weld;
(9) The weld between the furnace tube and the tube sheet is subjected to ash cleaning and polishing treatment until it is confirmed by coloring that no crack has been eliminated;
(10) The hydraulic pressure test is carried out on the boiler. The test pressure is 1.5 times of the working pressure of the boiler. The water pressure test checks that there is no leakage and pressure for 15 minutes, and no pressure drop is qualified;
(11) Delivery shipowner and ship inspection and receipt;
(12) Clean up the site, close the door of the smoke box, install the original disassembled attachment, and repair it.
Two, boiler tube welding process
(1) Cut off the old pipe, clean the water chamber, and grind the pipe joint or the old welding foot to the flat surface of the tube plate with an angle grinder. After welding the individual damaged parts, use an axial polishing machine to round the ball to eliminate oxidation. Iron and clean.
(2) Install the furnace tube in batches. When installing, the nozzle should extend 5-6MM of the tube plate to facilitate the welding operation;
(3) The job welder should hold the qualification certificate and should strictly abide by the welding process requirements. Manual arc welding, DC reverse connection. The electrode has a diameter of 3.2mm and the grade SH507. The welding current is 80 to 90 A and the voltage is 24 to 26 V. The welding speed is 10cm/min, and the welded right angle side is at least larger than the pipe wall thickness of 0.5-1MM. See the welding structure diagram shown in Figure 1 to prevent defects such as porosity, weld bead and incomplete penetration, and ensure the weld strength.
(4) The welding structure is shown in Figure 3.
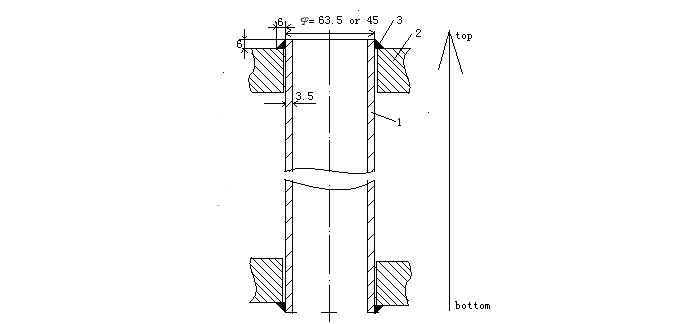
1.Boiler tube , 2. Tube sheet , 3. Weld seam
(5) Remove the solder coating, check the weld, and stain the flaw.