Welding process of ASTM A335 P91 Pipe
ASTM A335 P91 steel pipes have been widely used in the main steam pipes of large power stations in China in recent years because of its good high temperature comprehensive properties.
A335 P91 steel is widely used in the construction of many large-scale thermal power plants in recent years. A335 P91 steel is a new martensitic heat-resistant steel developed in the late 1970s and early 1980s in the United States, which is equivalent to 9cr-1mov steel made in China. Compared with domestic steel, A335 P91 steel has the characteristics of high temperature strength, good oxidation resistance, creep resistance, relatively high thermal conductivity and low thermal expansion rate, which fills the gap between ferritic steel (such as ASTM P22) and austenitic steel, and makes welding With a smaller section size, the thickness of weldment wall is effectively reduced, the amount of material is reduced, the thermal stress of pipeline is reduced, and the risk of thermal fatigue crack is reduced.
Assembly sequence of A335 P91 pipeline also plays a key role in welding quality. In order to ensure that the welding process and welding quality of A335 P91 steel pipeline meet the requirements, the welding process qualification must be made according to the welding characteristics of P91 steel, and the qualification report shall be taken as the basis for field installation and welding construction, and the process requirements shall be strictly implemented in the field construction process.
Weldability analysis of ASTM A335 P91 pipe
Chemical Composition of ASTM A335 P91
Grade | C | Mn | P | S | Si | Cr |
A335 P91 | 0.08-0.12 | 0.3-0.6 | ≤0.02 | ≤0.01 | 0.2-0.5 | 8.0-9.5 |
Mo | V | N | Ni | Al | Nb | |
0.85-1.05 | 0.18-0.25 | 0.03-0.07 | ≤0.4 | ≤0.04 | 0.06-0.10 |
According to the data in the table, this steel belongs to medium alloy heat-resistant steel.]
In alloy steel, in addition to carbon elements, other elements also play an important role in the strength and weldability of steel pipes. The carbon equivalent of A335 P91 refers to the welding carbon equivalent, which is calculated according to the following formula:
Ceq=C+Mn/6+(Cr+V+Mo)/5+(Cu+Ni)/15
Where CEQ is carbon equivalent
Therefore, the carbon equivalent of A335 P91 pipe CEQ = C + Mn / 6 + (Cr + V + Mo) / 5 + (Cu + Ni) / 15 = 0.08 + 0.30 / 6 + (8.0 + 0.18 + 0.85) / 5 + 0.4 / 15 = 1.9627
The middle value of carbon equivalent is 0.45. The smaller the corresponding carbon equivalent value is, the better the welding performance is. On the contrary, when the carbon equivalent value is larger, the worse the welding performance is. From the above calculation results of carbon equivalent of A335 P91 pipeline, it can be seen that 1.9627 is much larger than 0.45, so the welding performance of A335 P91 pipeline is poor.
Welding characteristics of A335 P91 steel
① A335 P91 is medium alloy steel, it has a rather high tendency of cold cracking. Under the condition of no preheating, the welding crack reaches 100%. When preheating for 200-250 ℃, the cold crack can be avoided.
In the process of welding, it is the first task to strictly control the interpass temperature of weldment and keep it at preheating temperature or higher. Secondly, pay attention to the time interval from the interlayer temperature cooling to the beginning of PWHT.
③ the requirement of controlling the input heat of welding is relatively high. The practical experience proves that the impact toughness can be greatly improved by using smaller electrode diameter, lower interlayer temperature and smaller welding line energy.
④ the welded joints are unstable structures with high hardness after welding, and corresponding heat treatment must be carried out after welding.
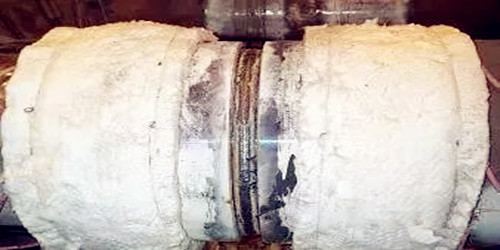
Selection of welding method
A335 P91 steel has a high hardening tendency and is very sensitive to welding cold cracks. It can be welded by TIG backing, low hydrogen electrode filling and covered electrode arc welding.
Welding procedure specification and parameters
Groove type:
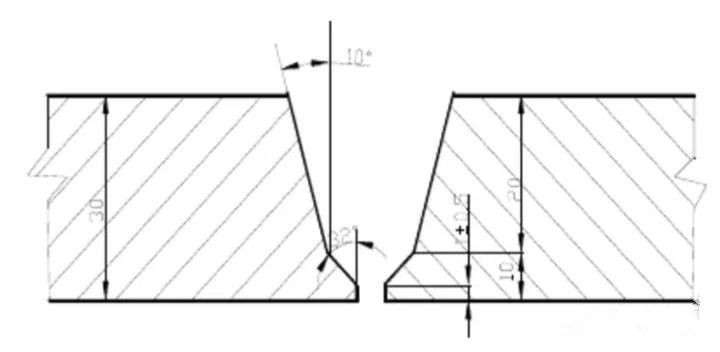
Welding parameters
Layer number | Welding method | Welding material | Welding parameters | |||
Model | Specifications | Polarity | Electric current(A) | Voltage(V) | ||
1~2 | GTAW | ER90S-B9 | Φ2.5 | Direct current connection | 90~110 | 10~14 |
3~6 | SMAW | E9015-B9 | Φ3.2 | DC reverse connection | 100~120 | 20~24 |
7 levels or more | SMAW | E9015-B9 | Φ4.0 | DC reverse connection | 135~150 | 20~24 |
Cover layer | SMAW | E9015-B9 | Φ3.2 | DC reverse connection | 100~120 | 20~24 |
Shielding gas: argon, purity ≥ 99.99%, argon flow: 8-12l / min for welding gun, 10-25l / min for the first pass on the back, 3-8l / min for the second pass.
Interlayer temperature: < 250 ℃ (temperature controlled by far infrared detector).
Post heat treatment: temperature rise to 300-350 ℃ after welding, and heat preservation for 2h.
Heat treatment: temperature 750 ℃ - 770 ℃, holding time 5min / mm, and not less than 4H; rise and fall temperature of post weld heat treatment is less than 150 ℃ / h.
According to the above process, the Φ 273 × 30 test pieces, which are fixed horizontally and vertically, are welded. After inspection and inspection, they all meet the specification requirements.
Welding construction process
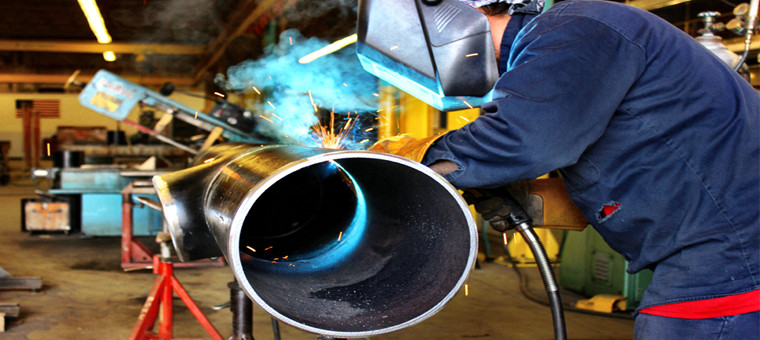
On the basis of qualified process assessment, relevant welding operation instructions are prepared in time according to the process assessment report. The content of P91 steel welding operation instruction is as follows:
Preparation before welding
1. Selection of welding materials er90s-b9 welding rod e9015-b9
2. The groove processing groove shall be machined, the groove shall be smooth and uniform, and the size shall meet the requirements. Before butt joint, it shall be carefully inspected. If it is found that it is unqualified, it must be polished to qualified with a polishing machine and other tools. Clean the rust, oil stain and other dirt within the range of 15-20mm on both sides of the inner and outer walls of the groove until the metal luster is exposed.
3. The special butt fixture shall be used for butt joint, which shall not be assembled by force. The inner wall shall be flush during butt joint. If there is a wrong joint, the amount of the wrong joint shall not exceed 10% of the wall thickness, and shall not exceed 1mm. Before butt joint, the base metal at the groove shall be carefully inspected for defects, and if there is any, it shall be treated separately. The welding materials, welding process and technical conditions of the selected welder for spot welding shall be the same as those for formal welding When the diameter thin-walled pipe is spot welded, the clearance is 2-3mm, which can be directly fixed in the groove by 2-3 points. When the large-diameter pipe is spot welded, the clearance is 3-5mm, which can be fixed by "positioning block".
Preheating before welding
The computer temperature control equipment shall be used to track and preheat the welded junction. The thermocouple shall be arranged symmetrically. The thermocouple and pipe fittings shall be in good contact. The preheating temperature of argon arc welding shall be 150-200 ℃, the preheating temperature of electrode arc welding shall be 200-250 ℃, and the preheating width shall be calculated from the pipe wall thickness at least 3 times of each side of the groove center.
Backing welding
Adopt WS-400 welding machine, DC positive connection. When the preheating temperature reaches the specified temperature and is even, the large diameter pipe is welded symmetrically by two people, and the first and second welding seams are all welded by argon arc welding. When welding the backing layer, the internal wire feeding method shall be adopted, and the root fusion shall be good, and the thickness shall be controlled within 2.8-3.2mm. In order to prevent root weld metal from oxidation, the pipe shall be filled with argon for protection.
Argon filling protection can be carried out according to the following requirements:
A. the scope of argon filled protection shall be subject to the groove center, 200-300 mm on each side, and the soluble paper or other soluble materials shall be used to make the sealed gas chamber with high temperature resistant tape.
B. insert "gas filling needle" from groove gap or "flaw detection hole" for argon filling. At the beginning, the back of argon flow is 10-25l / min, the back of the second pass is 4-8l / min, and the welding gun is 8-12l / min.
C. place the ignited lighter or match near the weld gap. When the flame goes out, it means that the internal air has been emptied. Argon arc welding can be used for backing welding.
Filling and covering welding of electrode arc welding
After the completion of argon arc welding, the preheating temperature shall be raised to 200-250 ℃, and the arc welding shall be started; the direct current reverse welding method and symmetrical welding of two persons shall be adopted. Because of the high viscosity, poor fluidity and small welding specification of molten iron in P91 steel, slag inclusion and lack of fusion between layers are easy to occur. Therefore, in order to avoid the occurrence of large defects and ensure the comprehensive mechanical properties of welded joints, multi-layer and multi-layer welding with small specifications must be adopted. The thickness of welding layer shall be as thin as possible, and the thickness of each layer shall not exceed 4mm. When swinging welding, welding rod shall be used The swing shall not exceed 4 times of the diameter of the electrode. Each layer of weld bead must be cleaned, especially the joint and both sides of the weld bead. After the welding of the weld surface is completed, the welder is required to carry out cleaning and self inspection immediately. If the appearance is not well formed, repair welding shall be carried out immediately. It is strictly prohibited to repair welding directly after the weld is cooled.
Post weld heat treatment
When the welding joint cannot be heat treated in time, the post heat treatment with the heating temperature of 300-350 ℃ and the constant temperature time of 2 hours shall be carried out immediately after welding.
The post weld heat treatment adopts multi output and multi-point temperature measurement, and the heater and thermocouple correspond one by one. The upper and lower temperature of the welding junction are consistent all the time, so that the heating and cooling speed of the welding junction of the heat treatment should be ≤ 150 ℃ / h. When the temperature is reduced to 300 ℃, it can be cooled to room temperature without control. The heating temperature is 750-770 ℃, and the constant temperature time is 5min / mm, but at least 4 hours.
Weld quality inspection
The weld quality shall be inspected according to the acceptance standard of class I weld. The inspection contents and requirements are as follows:
1. Appearance shall be inspected and accepted according to DL / t869-2004 technical code for welding of thermal power plant, quality standard of class I weld appearance;
2. NDT: 100% UT and MT inspection shall be carried out for welds according to JB4730, and grade I is qualified;
3. Hardness: after heat treatment, 100% hardness test shall be conducted, and the hardness value shall be less than 350hb;
4. Spectrum, 100% spectral analysis and recheck of weld metal alloy composition.
Weld repair
1. The appearance inspection of welded joint does not meet the standard. Polish and repair the light ones, and cut and re weld the serious ones.
2. For the unqualified welding joint through NDT, its defects can be repaired by welding, but on the basis of confirming that the defects have been completely eliminated, it must be carried out according to the normal welding process or welding repair process.
3. Generally, the same weld joint shall not be repaired more than twice, otherwise, it shall be cut and re butt welded.
4. The repaired welded joints must be subject to post weld heat treatment and NDT again.
Quality control
Strengthen the control of welding process of A335 P91 steel. Due to the poor welding performance of A335 P91 steel, the poor control of any link in the welding process will lead to poor mechanical properties of the welded joint and the generation of fatal defects such as cracks. First of all, all welders shall be trained and obtain the qualification certificate of A335 P91 steel before going on duty. Secondly, strict control shall be carried out from measures, materials, equipment, butt joints, welding, heat treatment parameters, surface quality of welded joints, NDT, repair of defective welds, etc.
Customer case
The 2 × 300MW Coal-fired Units for the expansion of No.3 and No.4 boilers in the second phase of Huaneng Power Plant are designed by Central South Electric Power Design Institute, and the boilers are produced by Dongfang Boiler (Group) Co., Ltd. with the model of DG1025 / 17.4 - Ⅱ 12. The steam turbine is produced by Harbin steam turbine Co., Ltd. with the model of subcritical primary intermediate reheat, single shaft double cylinder double exhaust condensing steam turbine. The design temperature of the main steam pipe, branch pipe and the pipe in front of the high bypass valve is 545 ℃, the pipe specifications are Φ 364 × 41, Φ 273 × 29 and Φ 216 × 23 respectively, and the material is A335P91.
Through the selection of the above construction technology, as well as strict technical and quality management measures, the appearance quality and joint surface hardness of main steam pipeline welds of boiler 3 and boiler 4 of Huaneng Power Plant Phase II project in this area all meet the standard requirements, and the one-time qualification rate of NDT reaches 100%. In addition, the weld quality is normal according to the water pressure test of the main steam pipeline of the power plant and the situation since it was put into operation.
Conclusion
The above welding process is effective for ASTM A335 P91 steel pipe. In addition, A335 P91 pipe is more cost-effective than A335 P22 pipe, which is widely used in the past. At present, it has become an inevitable trend to use P91 steel in large thermal power units.