Seamless Steel Pipe Piercing Process
Seamless steel pipe Piercing process
In the production process of seamless steel pipes, the Piercing process is widely used and very economical. In 1886, the German Mannesmann brothers applied for a patent for the production of tubular cross-section products using oblique roll piercers. The patent describes the effect of internal forces during metal deformation and the use of two or more tapered rollers for Piercing, so it is called the Mannesmann piercing process.
The guide plate invented by R.C. Stiefel increases the length of the pierced capillary. Later, Deschel invented the guide disc, which greatly improved the efficiency of Piercing. In 1970, there was a taper roll puncher, which had a significant improvement in metal deformation than previous punchers.
In the production of seamless steel tubes, the function of the piercing process is to pierce solid tube blanks into hollow capillaries. Piercing is the first process of metal deformation. The pipe that is penetrated has a thicker wall, a shorter length, and poorer inner and outer surface quality. Therefore, it is called a capillary. If there are some defects on the capillary tube, it will be difficult to eliminate or alleviate it after the subsequent process. Therefore, the Piercing process plays an important role in the production of steel pipes.
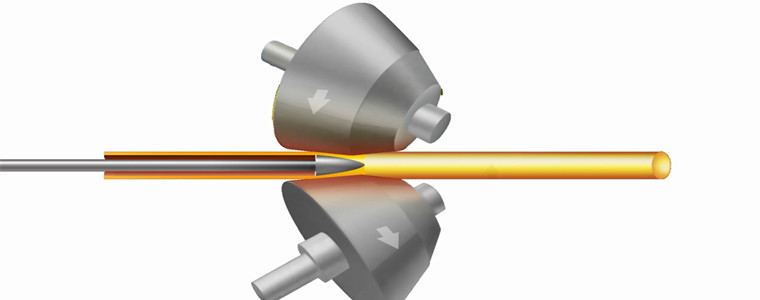
The piercing process is more reasonable in the production of seamless steel pipes today, and the piercing process is automated. The whole process of diagonal rolling piercing can be divided into three stages
The first unstable process is the stage where the metal at the front end of the tube blank gradually fills the deformation zone, that is, the tube billet comes into contact with the roll (one bite) until the front metal exits the deformation zone. This stage has one bite and two bites.
Stabilization process-this is the main stage of the piercing process, from the metal at the front end of the billet to the deformation zone until the metal at the end of the billet begins to leave the deformation zone.
The second unstable process is that the metal at the end of the tube blank gradually leaves the deformation zone until the metal completely leaves the roll.
There is a clear difference between the stable process and the unstable process, which is easy to observe in production. For example, there is a difference between the size of the head and tail of a capillary and the middle size. Generally, the diameter of the front end of the capillary is large, the diameter of the tail end is small, and the middle part is the same. The large size deviation between head and tail is one of the characteristics of unstable process. The reason for the large diameter of the head is that the front end metal gradually fills the deformation area, and the friction force between the metal and the roll contact surface gradually increases, and the maximum value is not reached until the deformation area is completely filled, especially when the front end of the tube blank and the plug When encountering, due to the axial resistance of the plug, the metal's axial extension is subjected to resistance, which reduces the axial extension deformation, and the lateral deformation increases, plus the absence of outer end restrictions, resulting in a large front end diameter. The small diameter of the end is because when the end of the tube blank is penetrated by the plug, the resistance of the plug is significantly reduced, and it is easy to extend and deform. At the same time, the lateral spreading is small, so the outer diameter is small.
The front and rear cards that appear in production are also one of the unstable characteristics. Although the three processes are different, they are all realized in the same deformation zone. The deformation zone is composed of rollers, plugs, and guide plates (guide plates). See Figure 4-1.
It can be seen from the figure that the entire deformation zone is a more complex geometric shape. It can be roughly considered that the cross-section is elliptical, and the annular deformation zone is reached when there is a head in the middle. On the longitudinal section are two cones connected by a small bottom, with an arc-shaped tip inserted in the middle.
The shape of the deformation zone determines the deformation process of the Piercing. Changing the shape of the deformation zone (decision and tool design and mill adjustment) will lead to changes in the deformation process of the pierce. The perforated deformation zone can be roughly divided into four sections, as shown in Figure 4-2.
Zone I is called the piercing preparation zone, (rolling solid round tube billet zone). The main function of zone Ⅰ is to prepare for the Piercing and achieve the second bite smoothly. The deformation characteristics of this section are: due to the tapered surface of the entrance cone of the roll, the tube blank that is advancing along the piercing direction is gradually compressed in diameter, and part of the compressed part of the metal flows laterally, and the wave surface of the blank has a circular shape that becomes elliptical. A part of the metal extends axially, which mainly deforms the surface metal, so a "flare" -shaped depression is formed at the front end of the blank. This depression and centering hole ensure that the nose of the plug is aligned with the center of the blank, thereby reducing the uneven wall thickness at the front end of the capillary tube.
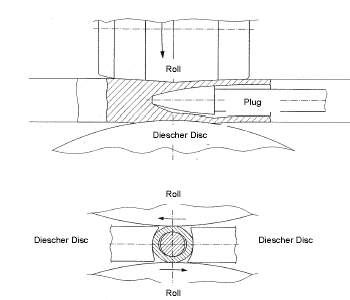
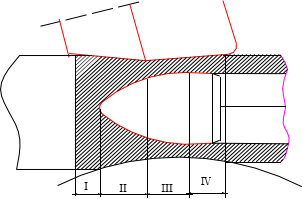
Zone Ⅱ is called the perforated area. The function of this area is to perforate, that is, the solid blank becomes a hollow capillary. The length of this area is from the encounter of the metal and the plug to the conical tape of the plug. The deformation feature of this section is mainly the wall thickness reduction. Since the distance between the roll surface and the plug surface is gradually reduced, the capillary wall thickness is rotated while being pressed, so it is a continuous rolling process. Deformation parameters are expressed in terms of relative reduction in diameter.Metals that are reduced in diameter can also flow laterally (diameter expansion) and longitudinally (extension), but lateral deformation is prevented by the guide disc, and longitudinal extension deformation is the main . The function of the guide disc can not only limit the lateral deformation but also pull the metal to extend in the axial direction. As a result of the lateral deformation, the cross section is elliptical.
Zone Ⅲ is called the rolling zone. The role of this zone is to smooth the rolling, improve the dimensional accuracy of the pipe wall and the quality of the inner and outer surfaces. Since the plug bus bar is approximately parallel to the roller bus bar, the reduction is very small, and it mainly plays the role of leveling. The cross-section of the rolled product is also oval in this section and gradually decreases.
Zone Ⅳ is called the rounding zone. The function of this area is to reduce the reduction of the diameter of the elliptical capillary tube by the rotating roller to zero, and to round the capillary tube. The length of this area is very short. The deformation in this area is actually a hollow capillary tube without a head. Plastic bending deformation, the deformation force is also very small.
The four sections are related to each other during the deformation process, and they are carried out simultaneously. The deformation process of the metal cross section is from the circle to the ellipse and then to the circle, see Figure 4-3.
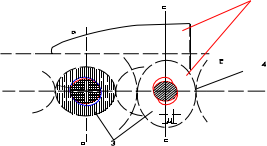