Testings for steel pipes
Testings for steel pipes
Steel pipes are not only used to transport fluids and powdered solids, exchange heat, manufacture mechanical parts and containers, but are also an economical steel. The use of steel pipes to manufacture building structure grids, pillars and mechanical supports can reduce weight, save 20-40% of metal, and achieve mechanized construction.
Therefore, in order to meet the needs of the use of steel pipes, we must carry out strict inspection of steel pipes.
Testing & Inspection items for steel pipes
Below are common test items for steel pipes.
1.Tensile strength test
The tensile test of steel tubes is a test method for determining the characteristics of steel tubes under axial tensile load. The elastic limit, elongation, modulus of elasticity, proportional limit, area reduction, tensile strength, yield point, yield strength and other tensile properties of steel tube can be determined by the data obtained from tensile test.
Creep data can be obtained from tensile tests at elevated temperatures.The steps of steel tube tensile test can be seen in ASTM E-8 standard.
Tensile test
The test of a series of characteristics of steel tube under tensile load is also known as tensile test. It is one of the basic methods for testing the mechanical properties of steel pipes. It is mainly used to check whether the steel pipes meet the prescribed standards and to study the properties of the materials.
Performance index
Steel tube tensile tests can be used to determine a series of strength and plasticity indexes of steel tubes. Strength usually refers to the ability of steel pipe to resist elastic deformation, plastic deformation and fracture under external force.
Tensile strength
When the steel tube is subjected to tensile load, the phenomenon that plastic deformation continues to occur without increasing the load is called yield. Yield stress is called yield point or physical yield strength. In engineering, there are many materials without obvious yield point, and the stress value of 0.2% residual plastic deformation produced by steel tube is usually regarded as yield strength, which is called conditional yield limit or conditional yield strength.
The maximum stress value of steel pipe before breaking is called tensile strength or strength limit.
Steel pipe plasticity
Plasticity refers to the ability of steel pipe to produce plastic deformation without failure under load. The commonly used plastic indexes are elongation and section shrinkage.
(1) Elongation, also known as elongation, refers to the percentage of the total elongation to the original length ratio of the steel tube material specimen after fracture under tensile load.
(2) Section shrinkage ratio is the percentage of the area reduced by the section to the area of the original section of the steel tube specimen after being pulled apart under tensile load.
NOTE:Yield strength, tensile strength, elongation and section shrinkage are the four performance indexes which are often measured in tensile test.
In addition, the elastic modulus, proportional limit and elastic limit of the steel tube can be determined.
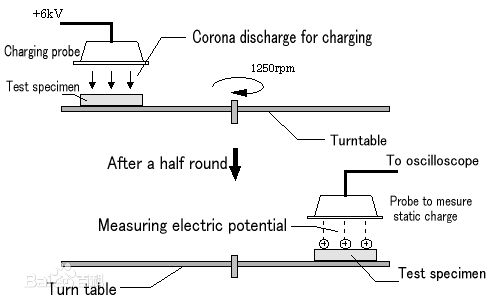
Test method
The steel tube tensile test is carried out on the material testing machine. The testing machine has mechanical, hydraulic, electro-hydraulic or electronic servo type.
The specimen preparation of steel tube should avoid the influence of cold and hot working on the microstructure of the material, and ensure a certain degree of smoothness.
During the test, the test machine evenly draws the steel pipe sample at a prescribed rate, and the test machine can automatically draw the drawing curve. For low carbon steel tube and other plastic materials, when the specimen is stretched to the yield point, the force measuring pointer has obvious jitter, and the upper and lower yield points can be separated. When calculating, the elongation and section shrinkage of the steel tube can be often taken to connect the specimen after fracture, and the elongation and section shrinkage can be measured and calculated.
2. Hot yield test
3. Impact test at different temperatures
Temperature impact test of steel pipe
The purpose of temperature impact test of steel pipe is to determine whether the performance of steel pipe fails when it is subjected to a series of impacts at normal and ultimate temperatures.
Temperature impact test, also known as cold and hot impact test or high and low temperature impact test, is used to test the adaptability of steel tube products to the rapid changes of ambient temperature. In some cases, it can also be used for environmental stress screening test.
Temperature impact test
The normal temperature impact test is conducted at room temperature, usually within 23 + 5 degrees.
Low temperature impact test; Store in low temperature medium for a certain period of time, make the temperature meet the requirements of rapid removal to complete the impact test.
(1) use medium can be ice water mixture (0 degrees Celsius)
(2) Other temperatures can be kept in a cryogenic tank. Alcohol or liquid nitrogen can be used to keep the sample warm at different temperatures.
The general standard of temperature impact test does not mention or stipulate the initial temperature of temperature impact test, but this is a problem that must be considered when the test is carried out, because it involves whether the test is finished at low or high temperature, thus deciding whether it is necessary to dry the steel pipe, resulting in prolonging the test time.
If the standard product is removed from the cold and hot impact test chamber at the end of the test, it should be restored under normal atmospheric conditions until the steel pipe sample reaches a stable temperature. This operation will inevitably lead to condensation introduction temperature on the surface of the test steel pipe sample. Thus changing the nature of the test.
4.Hydraulic test
Hydrostatic testing is a method in which pressure vessels such as pipes, cylinders, boilers and fuel tanks can be tested for strength and leakage.
Hydraulic testing involves filling containers or piping systems with liquids, usually water, which can be stained to aid visual leak detection and pressurized to a specified test pressure. The pressure seal can be tested by closing the supply valve and observing whether there is a pressure loss. If water contains colorants, it is easier to visually identify the location of the leak. The strength is usually measured by measuring the permanent deformation of the pipe or container.
Abstract
Hydrostatic test is carried out under the restriction of industry or customer specifications, or may be prescribed by law. A tube or container containing almost incompressible liquids, usually water or oil, is pressurized to test pressure and to check for leaks or permanent changes in shape. Red or fluorescent dyes can be added to the water to make the leak easier to see. Test pressure is always a higher safety factor than operating pressure. The safety factor is usually 166.66%, 143% or 150% of the design working pressure, depending on the applicable regulations.
Purpose of hydraulic test
Hydrostatic test is the most commonly used method for testing pipelines and pressure vessels. Using this test helps maintain the safety standards and durability of steel pipes.
Pipeline testing
Hydraulic tests of pipes, pipes and containers are performed to expose previously undetected defective materials, to ensure that any remaining defects are insufficient to allow operation under design pressure, to expose possible leaks, and to serve as a final verification of the integrity of the construction system.
Strength is measured by pressurizing it at any point in the pipe length to at least 125% of its maximum allowable working pressure (MAWP). Because many long-distance pipelines are designed to have a steel hoop stress of 80% of the specified minimum yield strength (SMYS) at maximum permissible working pressure MAOP, this means that the steel is subject to SMYS and above stress during testing, and the testing part must be selected to ensure that no excessive plastic deformation occurs.
If the design temperature of the steel pipe is higher than the test temperature, the test pressure must be adjusted according to the relevant allowable stress at the design temperature. This is achieved by multiplying 1.5 MAWP by the ratio of the allowable stress at the test temperature to the allowable stress at the design temperature.
Hydrostatic test procedure:
(1) Fill the pipe or container with water until the gas is exhausted and the surface of the pipe is dried.
(2) During the test, the pressure should be slowly increased to the design pressure. After confirming that there is no leakage, the pressure should be raised to the prescribed test pressure for 30 minutes, and then the pressure should be reduced to 80% of the test pressure. All welds and joints should be inspected for a long enough time.
(3) If any abnormal phenomena such as leakage, abnormal noise, pressure drop, failure of pressurizing device are found in the test, the pressure should be slowly lowered to zero and the test should be stopped immediately to find out the cause and eliminate the hidden danger before proceeding.
(4) Qualification requirements: no abnormal sound, no visible abnormal deformation, no leakage of weld and joint during the test.
5.Bending test
Pipeline bending tests deform the test pipes at the midpoint, resulting in concave or bending without fracture, and bending tests are usually performed to determine ductility or fracture resistance of the pipes. Pipe bending test is one of the basic methods for mechanical performance test of pipelines.
The purpose of pipe bending test:
Pipeline bending test is to deform the sample into a specific shape, which can determine the ductility, bending strength, fracture strength and fracture resistance of the pipeline. These characteristics can be used to determine whether the pipeline fails under pressure. If the pipeline begins to break or completely break during three or four point bending tests, it is assumed that the pipeline will fail under similar conditions in any application, which may lead to catastrophic failure.
There are four common types of bending tests.
(1) In the steering bending test, the sample is placed horizontally on two supports, and then applied to the top of the point to deform the sample into a "U" shape.
(2) in the semi guide bending test, the midpoint of the specimen is bent to a specific angle or radius.
(3) in the free bending test, the end of the sample is pushed together, but no force is applied to the bending itself.
(4) Finally, the common fracture toughness test (ASTM E399) consists of a sample with a pre-cracked actuator crack at the bottom of the midpoint and loaded into a three-point bending fixture so that the midpoint force is applied to the other side. Crack.
Advantages of bending test
(1) Three kinds of circular, square and rectangle are suitable for the measurement of inconvenient brittle materials.
(2) Tensile tests on brittle materials show little deformation. Bending tests can be used to express the plasticity of brittle materials with deflection.
(3) In the bending test, the stress distribution on the section is the largest on the surface, so it is sensitive to the surface defects of materials.
(4) For high plasticity material, bending test usually can not reach its failure degree, so bending strength test is not generally done.
(5) Bending test is simple and convenient.
6.Flaring test
Flaring test of steel pipe is a test method to test the deformation behavior of steel tube from radial expansion to specified diameter and to show its defects.
The pipe flaring test is suitable for measuring the plastic deformation ability of circular cross-section pipe flaring with an outer diameter not exceeding 150 mm (non-ferrous metal pipe not exceeding 100 mm) and a wall thickness not exceeding 10 mm. It is suitable for seamless pipe and welded pipe. It is also possible to negotiate with users about non-standard tests for external diameter and wall thickness.
Test Principle: Expanding one end of the pipe with conical plug until the maximum outer diameter of the enlarged end reaches the value specified by the relevant product standards.
Purpose of flaring test
The flaring test is a method to test the deformation performance of the pipe end flaring process. During the flaring test, the top core with a certain taper (such as 1:10, 1:15, etc.) is pressed into one end of the metal pipe sample to evenly expand to the flaring rate (%) stipulated by the relevant technical conditions, and then the flaws such as cracks are checked to determine whether the pipe is qualified or not.
Method of steel tube flaring test
(1)According to the relevant technical conditions or the provisions of the agreement between the two sides, different taper of the plug core is selected, and the recommended plug angle is 30, 45 and 60 degrees.
(2) tests should generally be carried out within room temperature. The strict temperature test should be controlled at (23 + 5) centigrade.
(3) Apply force to the conical plug smoothly to make the end of the steel pipe specimen flared evenly until the required diameter is reached. The maximum external diameter or expansion ratio of the specimen should be specified by the relevant product standards.
(4) allow lubrication of the top core. The speed of the plug core pressing into the steel pipe specimen is not stipulated generally, but the plug core pressing rate should not exceed 50 mm/min in case of dispute or arbitration test. The expansion test results shall be evaluated according to the requirements of the relevant product standards. If no specific requirements are specified, the specimens without visible cracks after testing should be assessed as qualified, only slight cracks at the edges of the specimens should not be discarded.
Characteristics of flaring test
(1) The expansion test process is similar to that of the material.
(2) Generally, the magnitude of stress is not considered, but the surface deformation after stress (such as cracks, cracks, etc.) and some characteristics specified after deformation are used to assess the quality of materials. The test results can reflect the plasticity, toughness and some quality problems of the material.
(3.)The test method is simple and does not require complex test equipment.
Therefore, the flaring test can be used as the delivery conditions according to the technical agreement. The test results can provide the basis for improving the casting, cold and hot working process of material production enterprises.
7.Ring tensile test
Ring tensile test of tubes
A method for a ring tensile test of tubes to reveal surface and internal defects.
Purpose of Ring tensile tes
By subjecting the test piece to strain until fracture occurs. This test may also be used to assess the ductility of tubes.
The ring tensile test is applicable to tubes having an outside diameter exceeding 150 mm and a wall thickness no greater than 40 mm. The inside diameter shall be greater than 100 mm.
Principle of Ring tensile test
Subjecting a ring cut from the end of a tube to strain in the circumferential direction until fracture occurs.
Apparatus of Ring tensile test
Two circular pins, of equal diameter with parallel axes, and movable in relation to each other while still remaining parallel.
In principle, the diameter of the pins shall be the minimum permissible from strength considerations but, provided that the inside diameter of the tube allows, should be at least 3 times the wall thickness of the tube to be tested (see figure 1).

(1)The test piece shall be a ring cut from the tube with the end faces perpendicular to the axis.
(2)The length of the test piece (width of the ring) shall be approximately 15 mm. If the thickness exceeds 15 mm, the length of the test piece may be equal to the thickness.
(3)The ends of the test piece shall be free from burrs. The edges may be rounded by filing or chamfered by other
NOTE — Non-rounded or non-chamfered edges are permissible, if the test result meets the test requirements.
Procedure of Ring tensile test
1.In general, the test shall be carried out at ambient temperature within the limits of 10 °C to 35 °C. The test carried out under controlled conditions shall be made at a temperature of 23 °C ± 5 °C.
2. Place the ring cut from the tube over the pins. Subject the ring to strain by moving the pins away from each other at a specified rate until it fractures. In cases of dispute, the rate shall not exceed 5 mm/s.
3.Interpretation of the ring tensile test shall be carried out in accordance with the requirements of the relevant product standard. When these requirements are not specified, the test piece shall be considered to have passed the test if no cracks are visible without the use of magnifying aids.
8.Ring bending test
9.Ring-expanding test
A method for a ring-expanding test on tubes, that is used to reveal defects bothon the surfaces and within the tube wall by expanding the test piece using a conical mandrel until fracture occurs. It may be also used to assess the ability of tubes to undergo plastic deformation.
The ring-expanding test is applicable to tubes having an outside diameter from 18 mm up to and including 150 mm and wall thickness from 2 mm up to and including 16 mm.
Principle of Ring-expanding test
Expanding a ring cut from the end of a tube, over a conical mandrel until fracture, or until the expansion of the test piece reaches a value specified in the relevant product standard (see figure 1).
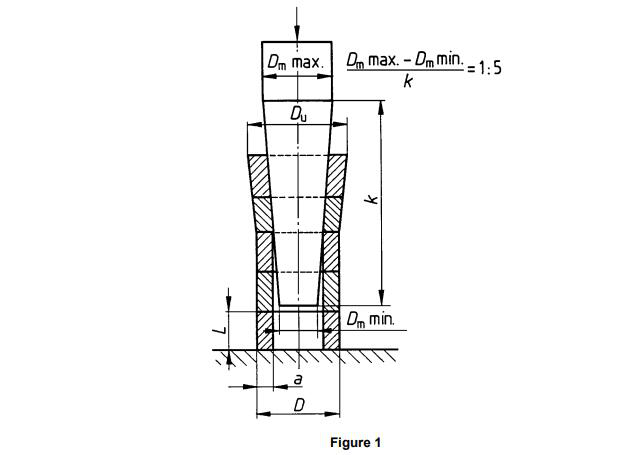
Apparatus
(1)Variable-speed press or universal testing machine.
(2)Conical mandrel, having a working length preferably tapered 1 : 5 as shown in figure 1, unless otherwise specified in the relevant product standard and its surface shall be of sufficient hardness, well-polished and free from scores.
Test piece
(1)The length of the test piece shall be between 10 mm and 16 mm. Test pieces shall be taken from the ends of deburred tubes as manufactured before they are cut to length. The rings shall be cut so that the planes of the end faces are parallel with each other and perpendicular to the axis of the tube.
(2)The edges of the test piece may be rounded by filing or chamfered by other methods.
NOTE — Non-rounded or non-chamfered edges are permissible, if the test result meets the test requirements.
(3)When welded tubes are subjected to the test, the internal weld flash may be removed.
Procedure
(1)In general, the test shall be carried out at ambient temperature within the limits of 10 °C to 35 °C. The test carried out under controlled conditions shall be made at a temperature of 23 °C ± 5 °C.
EN ISO 8495:2004 Licensed Copy: sheffieldun sheffieldun, na, Sun Nov 19 12:38:57 GMT+00:00 2006, Uncontrolled Copy, (c) BSI3
(2) Before testing, the rings and the conical mandrel may be lubricated. Rings of the same size and the same type of metal may be placed one on top of each other. The rings and the conical mandrel shall be concentric (seefigure 1).
(3)Force the conical mandrel into the rings until the required expansion is reached or the rings fracture.
(4)The rate of penetration of the conical mandrel shall not exceed 30 mm/s.
(5)The relative expansion shall be calculated in accordance with the relevant product standard.
(6) Interpretation of the ring-expanding test shall be carried out in accordance with the requirements of the relevant product standard. When these requirements are not specified, the test piece shall be considered to have passed the test if no cracks are visible without the use of magnifying aids.
(7) Test report
A test report shall be provided when so specified in the relevant product standard. In this case, the test report shall
include at least the following information:
a) reference to this International Standard, i.e. ISO 8495;
b) identification of the test piece;
c) dimensions of the test piece;
d) degree of expansion;
e) taper of the conical mandrel if different from that given in 4.2;
f) result of the test.
8. Hardness test
Steel tube hardness test is the quickest, most economical and simplest test method to evaluate the mechanical properties of steel tube. The main purpose of steel tube hardness testing is to determine the applicability of the steel tube, or the effect of special hardening or softening treatment for the purpose of use.
Hardness is one of the most commonly used indexes for evaluating the mechanical properties of steel tubes. The hardness is essentially the ability of the steel tube to resist the entry of another hard material. For the tested steel pipe, hardness represents the comprehensive properties of elasticity, plasticity, strength, toughness and wear resistance reflected by certain indenter and test force.
Principle of steel tube hardness test
The steel tube hardness test is to determine the hardness of the steel tube by slowly pressing a hard indenter into the surface of the steel tube specimen according to the prescribed conditions, and then testing the indentation depth or size. The hardness test is non-destructive, and there is an approximate conversion relationship between the hardness value and the tensile strength value of the steel tube. The hardness value of steel tube can be converted into tensile strength value.
Method for hardness testing of steel tubes
The determination of hardness is mainly determined by the depth of indentation, the area of indentation projection or the area of indentation gravure.
The main test method of steel pipe hardness testing, static test method, this kind of method test force is applied slowly without impact. Static test methods include brucelli, Rockwell, Vivtorinox, nu Shi, Wechsler and Pasteurella.
Brinell, Rockwell and Vickers test methods are the most widely used, they are the main test methods for steel tube hardness testing.
1) Brinell hardness
In seamless steel tube standard, Brinell hardness is the most widely used, and the indentation diameter is often used to express the hardness of the material, which is both intuitive and convenient. But it is not suitable for steel tubes with harder or thinner steel.
2) Rockwell hardness
The Rockwell hardness test of seamless steel tube is the same as Brinell hardness test. The difference is that it measures the depth of indentation. Rockwell hardness test is a widely used method at present, and HRC is second only to Brinell hardness HB in steel pipe standard. Rockwell hardness can be used to measure metal materials from very soft to very hard. It makes up for the shortcomings of Brinell method. It is simpler than Brinell method and can read hardness value directly from the dial of hardness machine. However, because of its small indentation, the hardness value is not as accurate as that of Brinell method.
3) Vivtorinox hardness
Vickers hardness test of seamless steel tube is also an indentation test method, which can be used to determine the hardness of very thin metal materials and surface layer. It has the main advantages of Brinell method and Rockwell method, and overcomes their basic shortcomings. But it is not as simple as Rockwell method, which is seldom used in steel pipe standard.
9.Spectral analysis
Spectral analysis of steel pipes is a method of identifying steel pipes and determining their chemical composition and relative content according to their spectra.
Spectral inspection is a kind of material analysis, and spectral analysis is one of the most common test methods to determine the chemical composition and content of steel pipe.
According to the analysis principle, spectral analysis can be divided into two types: emission spectrum analysis and absorption spectrum analysis.
Principles of spectral analysis
Emission spectrum analysis is based on the measured atom or molecule in the excited state of the emission of the characteristic spectrum intensity calculation.
Absorption spectroscopy is based on the characteristic spectra of the elements to be measured, through the sample vapor to be measured in the ground state atomic absorption spectrum of the elements to be measured after the intensity of the weakened calculation of its content.
Method
Firstly, the rust and other impurities on the surface of the steel pipe are ground off by a polishing machine, and then shot on the surface of the steel pipe by a spectral gun. The percentage of the chemical composition of the steel pipe is displayed on the display screen.
Advantages of spectral analysis
Spectral analysis is simple and accurate, and it is an indispensable and important analysis method for metal material inspection of power equipment.
10.Positive Material Identification (PMI) test
PMI test of steel pipe
The full name of PMI is Positive Material Identification, which refers to material analysis, or material identification, material chemical composition test.
PMI test of steel pipe mainly completes the content measurement and grade determination of each element in various alloy steel pipes. Judge whether the material of the steel pipe is up to standard. PMI testing is an important part of production. It ensures the safety of materials used in production.
There are three traditional methods of PMI test:
(1) Volumetric analysis: the standard solution (known concentration of the solution) reacts completely with the measured elements in the steel pipe, and then according to the volume of the standard solution consumed to calculate the content of the measured elements.
(2) Spectral analysis method: all kinds of elements can produce their own unique spectrum under the excitation of high temperature and high energy. According to the characteristic spectrum produced by the element after excitation, the chemical composition and the approximate content of the steel pipe can be determined. This method is called spectral analysis method. The characteristic spectra of the tested elements are usually excited by external energy such as arc, electric spark and laser. After spectroscopic analysis, the results were compared with those of chemical elements.
(3) Spark identification method: mainly used for steel, grinding in the grinding wheel, due to friction, high temperature, various elements, particle oxidation spark number, shape, bifurcation, color and other differences, to identify the material chemical composition (constituent elements) and roughly the content of a method.
Operation
The handheld alloy analyzer, which is widely used by people, is non-destructive, fast, quantitative, light and portable. Laboratory results can be obtained in a few seconds from the screen of a hand-held alloy analyzer, which plays an important role in field analysis. In many areas, hand-held alloy analyzer ensures 100% field material testing (PMI), is a very intuitive and convenient testing process, very popular with users.
Advantage
Hand-held alloy analyzer can quickly obtain alloy grade and chemical composition within 2-5 seconds without any shape and size restrictions on the part under test. Plates, fittings, flanges, welds, valves, wire meshes, etc. can be measured without restrictions, barrier-free, very low surface requirements, while the hand-held alloy analyzer system provides a strong user-friendly custom number and modification methods, users can freely adjust according to the use of habits and requirements.
Non-destructive tests include:
1.Ultrasonic test
Ultrasonic Testing is abbreviated as UT, also known as ultrasonic testing, ultrasonic testing of steel pipes is the use of ultrasonic technology to inspect the surface and internal quality of a means of testing, is one of the five conventional non-destructive testing methods.
Non-destructive testing is a means of testing the surface and internal quality of the inspected parts without damaging the working state of the workpiece or raw materials.
principle
Ultrasonic flaw detection of steel pipe is a non-destructive testing method to inspect the internal defects of steel pipe by using the reflection of ultrasonic wave and the energy change of penetration time caused by the acoustic performance difference between steel pipe and its defects.
Advantages and disadvantages of ultrasonic testing
The advantages of ultrasonic testing are large thickness, high sensitivity, high speed, low cost, harmless to human body, and can locate and quantify defects.
The disadvantage of ultrasonic testing is that it is not intuitive to the display of defects, it is difficult to detect defects, it is easy to be affected by subjective and objective factors, and the results of ultrasonic testing are not easy to preserve. Ultrasonic testing requires smooth working surface, and requires experienced inspectors to identify the types of defects, suitable for the inspection of parts with larger thickness. Ultrasonic flaw detection also has its limitations.
Ultrasonic testing process
Preparation before testing
(1)Familiar with the picked workpiece (workpiece name, material, specifications, groove form, welding method, heat treatment status, workpiece surface status, testing standards, qualified level, testing ratio, etc.);
(2) Selection of instruments and probes (determination of flaw detector, probe, test block, scanning ratio, detection sensitivity, detection mode according to the standard and field conditions)
(3) Calibration of the instrument (determination of horizontal and vertical linearity of the instrument when it is in use.)
(4) Calibration of probe (frontier, refraction angle, main beam deviation, sensitivity margin and resolution calibration).
(5)Instrument adjustment (the time baseline scale can be adjusted proportionally to represent the horizontal distance, depth or sound range of the pulse echo.)
(6)Sensitivity adjustment (sensitivity test is performed on the contrast block or other equivalent test block).
Detection operation
(1) Inspection of base material: Before inspection, the thickness of pipe wall should be measured, at least every 90 degrees, for reference. The two bottom wave of the defect free position is adjusted to the full scale of the fluorescent screen as the detection sensitivity.
(2) Inspection of welded joints: the scanning sensitivity should not be lower than the evaluation line (EL line) sensitivity, the scanning speed of probe should not exceed 150 mm/s, scanning adjacent two probe movement interval should ensure at least 10% overlap.
(3) test results and ratings: according to the nature of the defect, the magnitude of the indication length according to the relevant standards rating.
(4)Check and retest instruments and equipment.
(5)Issue test report.
Note: For welded joints with over-standard defects, the repaired parts and the affected areas should be re-inspected according to the original inspection conditions.
2. Magnetic Particle Examination (MPE) test
Magnetic particle testing of steel pipes
Magnetic powder detection
Magnetic particle testing is a method of observing material defects by using magnetic powder as the display medium. According to the kinds of magnetic powder medium applied during magnetization, the testing methods are divided into wet method and dry method; according to the time of magnetic powder applied on the workpiece, the testing methods are divided into continuous method and remanence method. Magnetic particle testing is one of the five conventional methods for nondestructive testing.
Purpose of magnetic particle testing
The detectable discontinuity width of magnetic particle detection can reach 0.1 M. Using a variety of magnetization methods, magnetic particle testing is almost independent of the size and geometry of the workpiece, and can detect defects in all directions of the workpiece.
Application scope of magnetic particle testing
1.is suitable for detecting surface and near-surface defects of ferromagnetic materials, such as cracks with very narrow surface and near-surface gaps and other defects that are difficult to see visually. It is not suitable for detecting deep internal defects.
2. It is suitable for testing ferromagnetic materials such as martensitic stainless steel and precipitation hardening stainless steel. It is not suitable for testing non-magnetic materials such as austenitic stainless steel.
3.It is suitable for testing raw materials (such as billets) and semi-finished products, finished products and workpieces in service and used.
4.it is suitable for detecting steel, bar, plate and forged steel castings and weldments.
5. It is suitable for detecting the defect that the direction of extension of the workpiece surface and near surface is as perpendicular as possible to the direction of magnetic line, but it is not suitable for detecting the defect that the angle between the direction of extension and the direction of magnetic line is less than 20 degrees.
6. it is suitable for detecting small defects on the surface and near surface of the workpiece, and is not suitable for detecting shallow and wide defects.
Magnetic particle testing of steel pipes
After the steel tube is magnetized, the magnetic flux leakage field is produced by the local distortion of the magnetic lines on the surface and near the surface of the steel tube due to the existence of discontinuity. The magnetic particles adsorbed on the surface of the steel tube form visual magnetic marks under appropriate light, thus showing the position, size, shape and severity of the discontinuity.
Advantages and disadvantages of magnetic particle testing for steel pipes
Advantages: non-destructive, simple and convenient operation, low detection cost, high sensitivity to steel tube surface and near surface defects detection, is the preferred method of steel tube surface defects detection.
Disadvantages: high requirements for the surface smoothness of the steel pipe, high requirements for the technology and experience of the inspectors, small detection range and slow detection speed.
Magnetic particle testing method for steel pipes
Wet process and dry process
Magnetic powder suspension in oil, water or other liquid medium is called wet method. It distributes magnetic suspension evenly on the surface of steel pipe in the process of testing. It shows the shape and size of the defect by the flow of liquid and magnetic flux leakage. Due to the dispersion and suspension performance of magnetic suspension, the particle size of magnetic powder can be smaller. Therefore, it has high detection sensitivity. It is especially suitable for detecting tiny surface defects, such as fatigue cracks and grinding cracks.
Dry method is called dry powder method. In some special occasions, when the wet method can not be used for testing, the special dry magnetic powder is applied directly to the magnetized steel pipe according to the program, and the defects of the steel pipe show magnetic marks.
Continuous method and remanence method
(1) Continuous method, also known as accessory magnetic field method or current magnetic method, is the magnetic particle or suspension applied to the steel pipe under the action of an external magnetic field for magnetic particle inspection. The observation and evaluation of steel tube can be carried out under the action of an external magnetic field or after interruption of magnetic field.
(2) remanence method, remanence method is to magnetize the steel pipe first, and then pour the suspension on the steel pipe, after the magnetic powder aggregation in observation. This is the method of detecting residual magnetism of steel tube, so it is called residual magnetism method.
3.Ferrite test
Ferrite test of stainless steel pipes
Ferrite measurement is a fast, cheap and accurate method for measuring the content of delta ferrite in austenitic and duplex stainless steel tubes. Proper ferrite content provides a balance between ductility, toughness, corrosion resistance and crack resistance.
Purpose of ferrite test
Heat, pressure and caustic environment require materials and welds with high metallurgical integrity. Correct ferrite measurement is helpful to avoid solidification cracks and corrosion of stainless steel welds, pipes, plates, pressure vessels and petrochemical components.
When ferrite content is too high, stainless steel will lose its ductility, toughness and corrosion resistance, especially at high temperature. If the ferrite content is too low, the weld of stainless steel will be affected by thermal crack or solidification crack.
In the weld of duplex stainless steel, the deficiency of ferrite content will also reduce the weld strength and contribute to the development of stress corrosion cracking.
Ferrite testing process
Baker testing can measure and report the ferrite content of welds and components during manufacturing and in-service using two different testing methods, depending on code or customer requirements. Using magnetic induction, trained BTS technicians can report readings individually or in a range to meet customer requirements through high-precision digital readings and on-site instrument calibration checks. In addition, high sensitivity and low MU permeability standards are used to measure ferrite content among a series of calibration standards. Test measurements can be reported by direct reading or conversion of the amount of ferrite (FN) or percentage of ferrite according to welding procedures, customer drawings and specifications.
4.Huye test
5.Eddy Current test
Eddy current testing of steel pipes
Eddy current testing is a kind of testing method which uses electromagnetic induction principle to detect surface defects of components and metal materials.
The advantages of eddy current testing are:
(1) The testing coil does not need to touch the workpiece, and does not need coupling agent. It is easy to realize high-speed and high-efficiency automatic testing for the detection of pipes, rods and wires. It can also be tested at high temperature, or the narrow area of the workpiece and the deep hole wall can be reached by the probe.
(2) high sensitivity to detect defects on the surface and near surface of the workpiece.
(3) Using different signal processing circuits to suppress interference and extract different eddy current influencing factors, eddy current testing can be used for conductivity measurement, film thickness measurement and metal sheet thickness measurement.
(4) Because the detection signal is an electrical signal, the detection results can be digitized, stored, reproduced, processed and compared.
Limitations of eddy current testing:
(1)It is only applicable to the detection of conductive metal materials or nonmetallic materials that can induce eddy currents.
(2) Because of the effect of eddy current penetration, it is only suitable for inspecting metal surface and near surface defects, and can not inspect the deep internal defects of metal materials.
(3)There are many factors that affect the eddy current effect. It is difficult for qualitative and quantitative analysis of defects.
(4)For different parts, there are deficiencies in using different test coils.
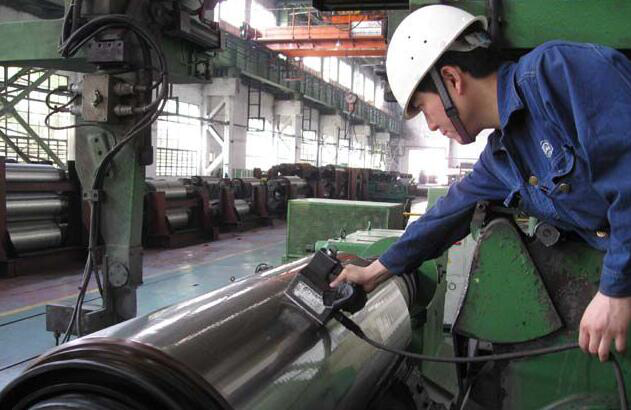
A flaw detection method for detecting the surface and near surface defects of steel tubes is developed based on the principle of electromagnetic induction.
The principle is that the eddy current is produced in the steel pipe by the excitation coil, and the change of eddy current is measured by the detection coil, so as to obtain the relevant information of the steel pipe defects.
According to the shape of the detection coil, it can be divided into three types: through type (for wire, rod and pipe detection), probe type (for local detection of component surface) and insertion type (for internal detection of pipe hole).
Method of Eddy current testing
Eddy current detection is to set up alternating magnetic field by coil when the conductor is close to the coil with alternating current. The alternating magnetic field passes through the conductor and induces electromagnetic induction with the conductor to set up eddy current in the conductor. The eddy current in the conductor also produces its own magnetic field. The effect of the eddy current magnetic field changes the strength of the original magnetic field, which leads to the change of the coil voltage and impedance. When a defect occurs on or near the surface of a conductor, the strength and distribution of the eddy current will be affected. The change of the eddy current will cause the change of the voltage and impedance of the detecting coil. According to this change, the existence of the defect in the conductor can be known indirectly.