Type Of Continuous Pipe Mill
Type Of Continuous Pipe Mill
The continuous pipe rolling machine is inserted into the long mandrel in the capillary tube, and is sequentially arranged through multiple stands and the adjacent rolls are staggered (the two rolls are staggered by 90 °, as shown in Figure 1; three rolls) Continuous rolling mills with roll gaps offset by 60 °) are rolled into steel pipes, which is the most widely used method of longitudinally rolled steel pipes today. During the rolling process of the continuous pipe mill, the deformation of the rolling stock is actually a process from circle to ellipse ... ellipse to circle, which is repeatedly affected by multiple groups (4 ~ 8 groups) of rollers and mandrel.
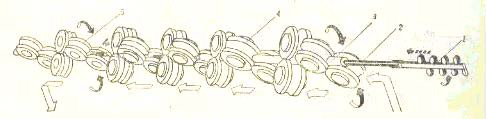
Figure 1 Process diagram of MPM pipe rolling
1-Mandrel stopper 2-Mandrel 3-Capillar 4-Continuous tube rolling machine 5-Dropper
1-Mandrel stopper 2-Mandrel 3-Capillar 4-Continuous tube rolling machine 5-Dropper
The continuous rolling mill has a long history. As early as the end of the 19th century, attempts were made to roll pipes on long mandrels, but for various reasons, by 1950 there were only 6 continuous rolling mills in the world. After 1960, with the advancement of science and technology and the development of production, especially the rapid development and application of electronic computer technology, the continuous rolling mill has become increasingly perfect in production technology and equipment, and has been rapidly developed and promoted. On the basis of the floating mandrel mill, the limited mandrel mill was tested in the mid-1960s and achieved gratifying results. In 1978, the world's first set of restricted mandrel continuous pipe rolling mill (MPM) was completed and put into operation at the Italian Dalmin Steel Pipe Plant, and the continuous rolling process has reached a new level. In the late 1990s, the three-roller continuous pipe mill (PQF) technology was introduced, which made the continuous rolling process equipment go to a higher level.
Before the emergence of PQF, continuous rolling mills were two-roller type, that is, two rolls constituted a group of holes. The two-roller frame was either staggered at 45 ° from the ground or perpendicular to the ground. Horizontally staggered; PQF is a three-roller type, that is, a set of three rolls constitutes a hole pattern; MPM and PQF hole patterns are formed (see Figure 2); when continuous rolling of tubes, the metal at the top of the hole pattern is subject to the rollers The external pressure and the internal pressure of the core rod cause an axial extension and widen laterally to the circumference. The metal of the hole-shaped side wall portion does not contact the core rod, but it is subject to the additional tensile stress of the metal extending axially at the top. The action results in an axial extension and at the same time an axial contraction. Regardless of the two-roller or three-roller continuous rolling mills, according to the operation mode of the mandrel, it can be divided into the following three forms.
1.Floating mandrel continuous rolling mill (or full floating mandrel continuous rolling mill)
2.Semi-floating (or semi-limiting) mandrel continuous tube rolling machine
3.Limiting mandrel continuous rolling mill
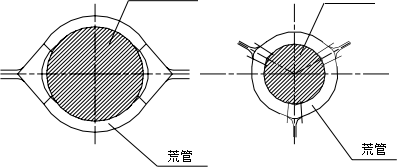
Fig. 2 Passive structure of continuous rolling pipe
1.Floating mandrel continuous rolling mill (or full floating mandrel continuous rolling mill)
Referred to as MM (Mandrel Mill). The speed of the mandrel is not controlled during the rolling process. The mandrel is driven by the friction of the rolled metal to freely follow the pipe through the rolling mill. The running speed of the mandrel is uncontrolled; during the rolling process, the speed of the mandrel varies with There are fluctuations in the biting and throwing of each frame, which causes fluctuations in the wall thickness of the pipe. After the rolling is finished, the core rod is rolled out with the waste pipe to the output roller table after the continuous rolling mill. During the rolling, the thin-walled pipe At this time, almost the entire length of the core rod is in the waste pipe, as shown in Figure 3; the waste pipe with the core rod is traversed to the stripping line, and the core rod is pulled out of the waste pipe by the stripper machine for cooling and lubrication and recycling. It is characterized by fast rolling rhythm, which can roll 4 or more steel pipes per minute; but the wall thickness accuracy of the waste pipe is slightly lower, the process of removing the rod is longer, and the length of the core rod is close to the length of the tube. ; Suitable for the production of seamless steel tubes of smaller specifications (less than 177.8mm outside diameter). The more representative floating mandrel mills are the RK2 unit of the Mülheim plant in Germany and the φ140 mm unit of Baosteel in China.
The working characteristics of the floating mandrel tandem rolling mill are: because the mandrel speed is not controlled during rolling, the mandrel speed changes many times during the entire rolling process. For example, on an 8-stand continuous pipe mill, when the metal enters the first stand, the core rod runs under the effect of friction at a rolling speed close to the first stand; when the metal enters the second stand The speed of the mandrel will change when the rack is moved, running at a speed between the rolling speed of the first and second stands; when entering the third stand, the mandrel speed has changed to the first, second and A certain speed between the rolling speed of the third frame; and so on, until entering the eighth frame, the mandrel speed has changed 8 times, running at a speed between 1 and 8 frames, entering a Relatively stable rolling stage. At this stage, the rolling speed of the front frame is slower than the speed of the mandrel (called the slow frame), and the rolling speed of the rear frame is faster than the speed of the mandrel (called the fast frame). The rolling speed of the rack is exactly the same as that of the mandrel. Later, when the metal is gradually rolled out of the relevant frame, the speed of the core rod changes to a speed between 2 and 8 frames; when the metal is rolled out of the second frame, the core rod speed becomes third to A speed between the eighth frame, and so on, until the metal is rolled out of the eighth frame.
It can be seen from the above that during the rolling process of the steel pipe, the speed of the core rod must be changed at least 15 times, and the change of the speed of the core rod will cause the change of the metal flow conditions. The floating mandrel continuous rolling mill changes the metal flow due to the change of the mandrel speed during the rolling process, and the vertical wall thickness and diameter of the steel pipe change due to the irregularity of the metal flow. Although many measures have been taken and obtained With a certain effect, when changes in rolling conditions still exist, and the dimensional accuracy of the product tube is always inferior to that of a mandrel rolling mill. In addition, the length of the mandrel increases the manufacturing cost, makes it difficult to manufacture, and the weight of the long mandrel is also very large. Running the steel pipe with an overweight mandrel on the roller table will cause damage to the surface of the steel pipe. Therefore, the floating mandrel continuous tube rolling mills are currently used for small units.
In continuous rolling, a rough tube can be regarded as being formed by continuous rolling between rolls of different diameters. The mandrel worn in the steel tube can be regarded as an inner roll with infinite curvature radius. When the floating mandrel is rolled, the mandrel has no external force except the force transmitted by the roll through the rolled product. After the head of the rolled product is bitten into the first frame, the number of frames acting on the mandrel increases one by one as the rolled material moves towards the rear extension frame one by one, so the speed of the mandrel increases continuously. This stage is called " Bite "stage. When the head of the rolled product enters the last stand, the entire rolled product is rolling in all stands of the continuous rolling mill, and the speed of the core rod remains unchanged, which is called the "stabilizing rush" stage. When the tail of the rolling stock leaves the first frame, the speed of the core rod increases gradually until the rolling out extension, which is called the "rolling out" stage. The working peripheral speed of the roll is set in the "steady rolling" state. During the rolling process, the rolled product follows the law of constant volume. However, the increase in the rolling speed caused by the core rod will inevitably increase the amount of metal flowing into the rear frame, that is, the rear frame is fed by the core rod more than the set peripheral speed of the roll allows. More metal, which leads to metal accumulation that increases the cross-sectional area. The larger section caused by this gradually flowing additional metal, despite being processed on the final frame, still leads to a larger diameter and thicker wall in some parts of the waste pipe. This phenomenon is called "bamboo joints" ". In principle, it is possible to have "bamboo joints" on the entire steel pipe. Obviously, the "bamboo joints" phenomenon is uneven vertical wall thickness, which is not good for subsequent rolling reduction and should be prevented as much as possible.
In order to prevent or reduce the formation of "bamboo joints", when the reduction design of the hole-type design distributes the reduction amount, the reduction amount of the first several frames is appropriately increased on the premise of ensuring that the total extension remains unchanged. In this way, the jump in the speed of the mandrel can be reduced in the following several frames, thereby reducing the impact of the speed change of the mandrel. Good mandrel lubrication is beneficial for extension and reduction of energy consumption, and it can also reduce the formation of sticks. Electric control technology can also be used to prevent the occurrence of bamboo shoots. Pre-set by an electronic computer, the rotation speed of the roll changes as required, and the roll is calibrated when the rolling stock passes, so that the exit speed of each stand is adapted to the change of the speed of the core rod.
In the 1970s, the floating mandrel mill was popular. Due to the limitation of the weight of the mandrel, so far this unit can only produce steel pipes with a diameter less than 177.8mm.
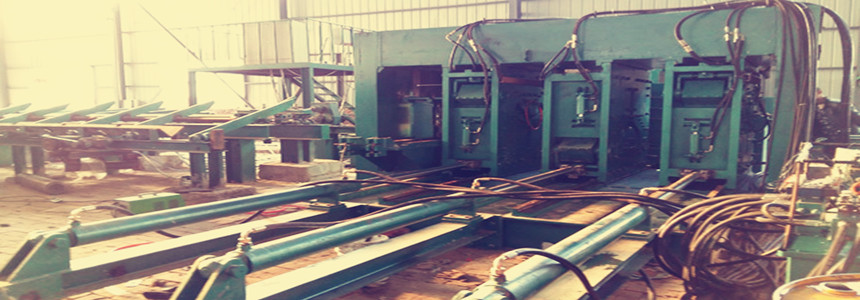
2.Semi-floating (or semi-limiting) mandrel continuous tube rolling mill
The German name is MRK-S (Mannesmann bohr-Kontimill Stripper); the French name is Neuval-R.
The German-designed process is: During the first half of the rolling process, the mandrel does not move freely with the rolled product, but is controlled by the moving mechanism. It advances at a constant speed. Inconsistent, the exit speed of the rolled product in the first frame is lower than the speed of the core rod; since the second frame, the speed of the rolled product is faster than the speed of the core rod, forming a stable differential rolling state;
When the main deformation is completed and the pipe is disengaged from the penultimate rack, the stop mechanism accelerates the release of the mandrel, and the mandrel is taken out of the rolling mill by a steel pipe like a floating mandrel. The German-style semi-floating mandrel mill was completed and put into operation at the Hachiman Plant in Japan in the early 1980s. The process developed in France is: the mandrel is only loosened when the steel pipe is rolled out from the last stand, that is to say, there is a limit during the rolling process.
The technical characteristics of the moving mandrel rolling mill, and the mandrel is loosened after the final rolling; the mandrel follows the waste pipe to the output roller table after the continuous rolling mill. The French-style semi-floating mandrel mill was put into production at the Saint-Sof steel pipe plant in France in the late 1970s.
Regardless of the German or French process, after the rolling of the semi-floating mandrel tube mill, about one-third of the waste pipe (tail) is wrapped around the front end of the mandrel, as shown in Figure 4; To the off-rod line, the mandrel is pulled out of the waste pipe by the off-rod machine for cooling and lubrication and then recycled. Its characteristics are high accuracy of wall thickness and fast rhythm. It can roll 3 or more steel pipes per minute. Although the length of the mandrel is much shorter than that of the floating type, it is slightly longer than that of the restricted mandrel rolling mill. ; It has a de-roding machine process which has a long process; suitable for the production of seamless steel tubes of smaller specifications (outer diameter less than 219mm). The representative units of the German model include the φ194 mm unit of the Hachiman Plant in Japan and the φ89 mm unit of Hengyang in China; so far, there is only one set of the French model unit, which is the φ127 mm unit of the Saint Ville factory in France
The semi-floating mandrel mill also controls the speed of the mandrel during the binding process, but the mandrel will be released before the end of rolling. Like a floating mandrel mill, the mandrel is taken out of the rolling mill by steel pipes. , And then the mandrel is pulled out of the waste pipe by the off-rod machine. When the mandrel speed is limited, the problem of the regularity of metal flow is solved to a certain extent. After the mandrel is released, the restrictions of the off-rod conditions are considered like the floating mandrel continuous tube rolling machine. Therefore, The diameter of the steel pipe rolled by the semi-floating mandrel mill should not be too large.
The semi-floating mandrel rolling mill takes into account the advantages of the restricted mandrel and floating mandrel rolling mills. It not only maintains a high rolling rhythm, but also ensures the wall thickness accuracy and inner and outer surface quality of the steel pipe. The off-rod machine is installed so that the upper limit of the rolling specification is limited.
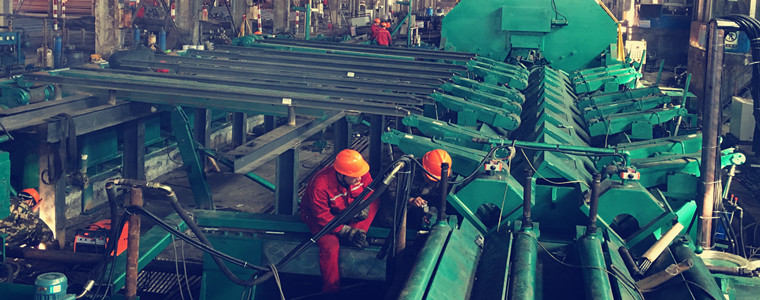
3.Restricted mandrel continuous rolling mill
Referred to as MPM (Multi-Stand Pipe Mill). During the rolling of the mandrel, the movement of the mandrel is limited and the speed is controllable; the speed of the mandrel should be higher than the bite-in speed of the first frame and lower than the roll-out speed of the first frame. The speed of the core rod is constant during the whole rolling process, so as to ensure the accuracy of the wall thickness of the tube. The speed of the core rod can be adjusted within a certain range when rolling different tubes. After rolling is finished, the mandrel is stopped, and the tube is removed from the mandrel by the tube stripper, and then the mandrel is returned from the rolling mill, and the rolling line is cooled and lubricated for recycling. It is characterized by high precision of the wall thickness of the waste pipe. The tube remover is used instead of the rod remover, which shortens the process flow and the core rod is short. ; Suitable for the production of medium-sized (less than 460mm) seamless steel pipes. Representative units include the φ356 mm unit of Darmin in Italy and the φ250 mm unit of Tianjin Steel Pipe Company in China.
In order to solve the problem of irregular metal flow during the rolling process of the floating mandrel continuous rolling mill, shorten the length of the mandrel, and solve the difficulties in the manufacture of the mandrel, the foreign countries began to test the restricted mandrel rolling in the 1960s. In the 1970s Success, industrial production at the Darmin plant in Italy.
The basic feature of the limiting mandrel continuous pipe rolling machine is to control the running speed of the mandrel, so that the mandrel advances at a constant speed lower than the metal rolling out speed of the first frame during the entire binding process, which is very important. The improvement of the process makes the limited mandrel rolling mill superior to the floating mandrel rolling mill. Practice in recent years has shown that the speed of the core rod should be higher than the bite-in speed of the first frame and lower than the roll-out speed of the first frame. In this way, the moving speed of the core rod is lower than the rolling speed of all the stands during the entire binding process, avoiding irregular metal flow and changes in rolling conditions. Because the mandrel speed is controlled, the rolling pressure of each stand is small, the metal flow is regular, and the elongation coefficient can reach some, which can obtain very good wall thickness deviation.
Due to the speed limit of the core rod, the length of the core rod can be greatly shortened. When a 32m steel pipe is rolled, the working length of the core rod is only 15m. After the steel pipe is rolled out from the mandrel, it is pulled out from the front end of the mandrel by a pipe stripper, and the mandrel returns quickly. Unlike the floating mandrel rolling mill, which is limited by the conditions of the mandrel removal, it can produce medium and large seamless Steel Pipe.
The restricted mandrel continuous tube rolling mill is developed on the basis of the floating mandrel continuous tube rolling mill. Compared with the floating mandrel mill, the limited mandrel mill has the following advantages:
1) Reduced tool consumption. The mandrel of the limited mandrel rolling mill is shorter than the mandrel of the floating mandrel rolling mill, and the contact time between the steel pipe and the mandrel is short, which increases the life of the mandrel and generally consumes the mandrel. Reduced to about 1 kg per ton of steel pipe.
2) Improve the quality of steel pipes. Due to the nature of the rolling mandrel rolling mill (relative movement of the mandrel and the inner surface of the steel pipe), it is beneficial to the extension of the metal. In addition, the rolling state with micro-tension reduces the lateral deformation and there is no floating at all. The "bamboo joint" phenomenon produced by the continuous rolling of the mandrel bar has greatly improved the inner and outer surface and dimensional accuracy of the steel pipe.
3) Eliminated the rod removal machine, shortened the process flow, and increased the final rolling temperature of the steel pipe. Some varieties can save the reheating process before sizing, thereby saving energy.
4) Expanded product specifications. Due to the use of restricted mandrel rolling, the length of the mandrel can be reduced, the weight of the mandrel can be reduced, the diameter of the mandrel can be increased, and the maximum outer diameter of the steel pipe can be expanded from 177.8mm to 426mm or more. The restricted mandrel continuous rolling mill can also roll steel pipes with a larger diameter-to-wall ratio (D / S> 40).
Restricted mandrel continuous rolling mill represents the advanced technology of modern seamless steel pipe production, which concentratedly reflects the continuous, high efficiency, mechanization and industrial automation development trends of seamless steel pipe production. Since the 1980s, it has dominated the field of seamless steel pipe production.
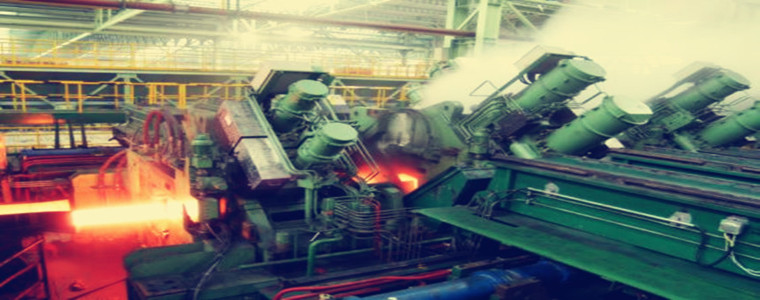
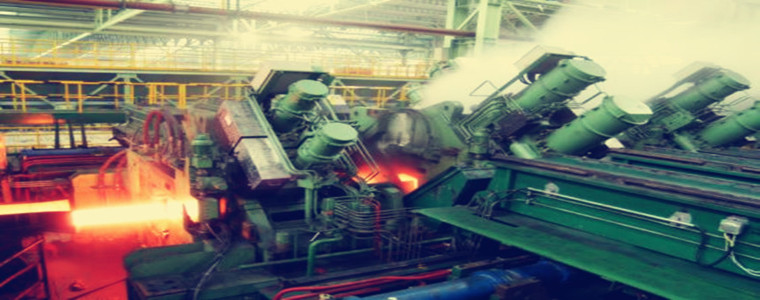
4.PQF ((Premium Quality Finishing)
It is also a restricted mandrel continuous tube rolling machine, except that each stand is composed of three rolls; the three-roll design has a better roundness than the traditional two-roll design, and the hole radius is worse It is small, which is beneficial to the uniform deformation of the rolling stock and the uniform wear of the roll. The difference in peripheral speed between the bottom of the rolling groove and the top of the rolling groove is small, so that the metal deformation during rolling can be more uniform under stable conditions. The flange area (the area of the tube that is not in contact with the roll or mandrel. That is, the wall thickness at the roll gap / the convex area of the outer warp) is reduced, that is, the amount of metal flowing to the flange is reduced. This advantage is particularly important when rolling the end of a steel pipe that is not constrained by the outer end and other stands. In fact, the end of the steel tube is controlled on the three-roller mill because of the small flange area (about 30% smaller than the two-roller) and the smaller peripheral speed difference between the bottom of the rolling groove and the top of the rolling groove. Sake. Therefore, it is possible to avoid or greatly reduce the tube end folding and the formation of fins. Due to the high circumferential compressive stress, the danger of longitudinal tensile stress at the roll gap during rolling can be greatly reduced. The stability of the mandrel in the hole type is high. The PQF unit can produce high-strength (above P110) special steel-grade oil well pipes, high-pressure boiler pipes, and 13Cr and 304L stainless steel pipes. The biggest advantage of PQF is that because the radius difference of the three-roller pattern is smaller than that of the two-roller, the deformation of the rolled product is more uniform and stable, which makes the wall thickness accuracy and surface quality of the product higher than MPM. The φ168mm PQF unit adopts a unique mandrel operation mode, which makes its rolling rhythm reach 24 seconds per support. The representative unit is the φ168 mm unit of Tianjin Steel Pipe Company.
There are two ways to run the mandrel of the restricted mandrel mill:
First, at the end of rolling, the mandrel stops moving. After the tube is removed from the mandrel, the mandrel returns quickly, the rolling line is pulled out, and it is recycled after cooling and lubrication. Traditional MPMs use this mode of operation.
The other operation mode is: at the end of rolling, the mandrel stops moving. After the waste pipe is taken out of the mandrel by the tube stripper, the mandrel is not returned, but runs forward quickly after the waste pipe and then passes the pipe After the mandrel passes through the tube stripper, the rolling line is pulled out and then returned, cooled, and lubricated. This method reduces the online waiting time of the mandrel (non-rolled steel). This effectively shortens the rolling cycle and speeds up the rolling rhythm. PQF uses this mode of operation;
The main difference between the two operation modes is that after the tube is removed, the mandrel is run in the opposite direction of the rough tube and backed out of the rolling mill. The rolling line is cooled, lubricated and recycled; or the mandrel runs in the same direction and leaves the mill After passing through the tube stripping machine, the rolling line is dialed out for cooling, lubrication and recycling. The second method requires the mandrel to pass through the tube stripper, and when rolling thin-walled tubes (reduced tube wall thickness of the tube stripper is greater than or equal to 2 times the wall thickness of the waste tube), the tube of the tube stripper must have a quick opening and closing function In order to prevent the mandrel from hitting the roll of the tube separator.